Corrosão. Quais os tipos de testes?
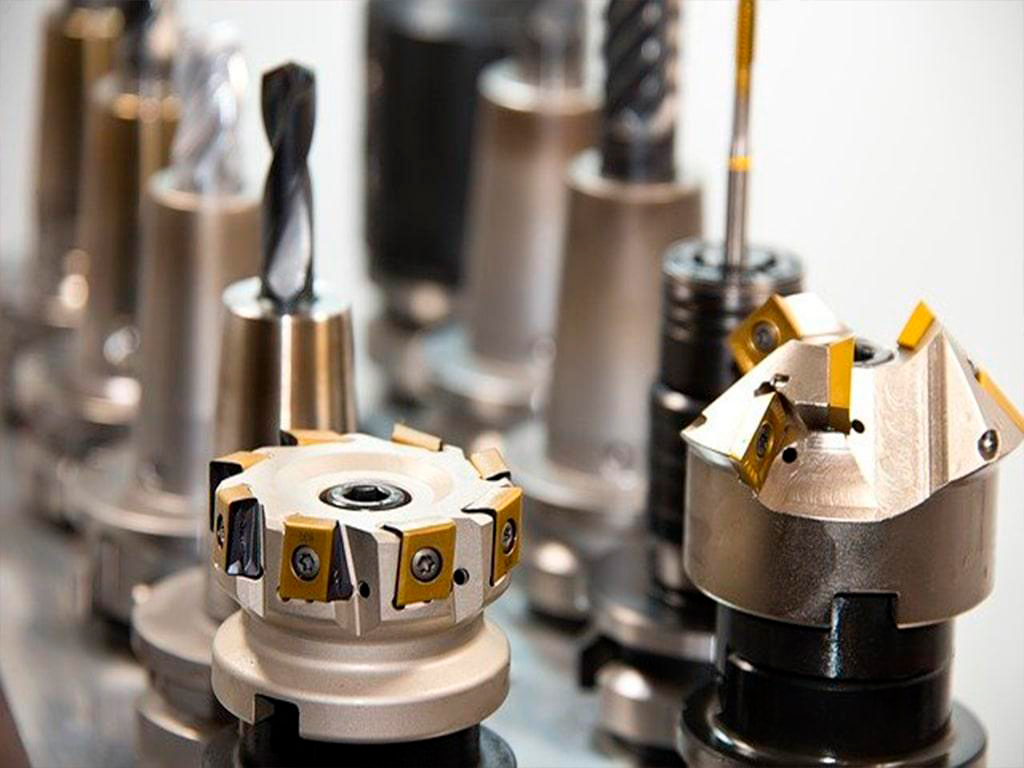
1 de maio de 2022
O Teste de corrosão é a interpretação dos resultados que pode ser um dos mais controvertidos
assuntos na indústria de galvanoplastia. Apesar disto, este é um dos mais importantes parâmetros tanto para aceitação como para rejeição de muitas galvanoplastias.TIPOS DE TESTES :
O teste de corrosão pode ser dividido em 3 categorias :
1) MOBILIDADE OU TESTE EM USO
Este, sem dúvida, seria o modo ideal de testar qualquer peça, desde que a severidade do teste e suas variáveis, seria a representativa mais exata do serviço em que a peça seria usada. Entretanto, esse tipo de teste tem duas grandes deficiências. O tempo necessário para obter a real informação, usualmente estende-se em anos e todo lugar exposto é diferente por exemplo “uma bomba testada na área de praia daria um resultado, enquanto que a mesma bomba testada em Campos do Jordão daria um outro resultado.
2) EXPOSIÇÃO ESTÁTICA
Visto que, é difícil a execução do teste acima, a melhor coisa a fazer em seguida seria expor a> peça de uma maneira que ela fosse testada como se estivesse em uso, mas com maior possibilidade de avaliação e estudo dos efeitos da corrosão. Por esta razão a exposição em lugares não móveis, pode ser estabelecida vários locais em vários tipos de atmosferas, como por exemplo, as atmosferas da costa do mar ou em localização de indústrias pesadas. Mesmo se os resultados forem representativos de uso real, o longo período de tempo para obter resultados significativos é definitivamente desvantajoso.
3) TESTES ACELERADOS
Muitos dos trabalhos feitos em testes de corrosão durante os últimos 15 anos, tem sido na área de acelerar o teste de corrosão.
Como o nome sugere, o objetivo desses testes são reproduzir os efeitos de corrosão em curto espaço de tempo, tal como 1 dia ou menos, que representaria um longo período de tempo em uso ou serviço, como por exemplo 1 ano de uso da peça.
Para este fim, os vários testes relacionados abaixo tem sido planejados e usados pelas indústrias. Seria muito extensivo descrever totalmente todos os parâmetros operacionais destes estes.
As descrições e as finalidades para a grande maioria destes testes são prontamente avaliadas na forma de modelos ASTM.
3.1. TESTE ACELERADO DE COBRE / ACIDO ACÉTICO SALT SPRAY (CASS) ASTM B-368. Neste teste é utilizada uma câmara de vapores dispersantes que distribui uma porcentagem determinada de cloreto de sódio, cobre e acido acetico glacial sobre a peça a ser tratada em um período de tempo predeterminado. Isto é a princípio aplicado como um teste rápido em cobre/níquel/cromo ou níquel/cromo, revestimentos de cromo em ferro e zinco diretamente para uso relativamente severo. Isto também é aplicado para teste de alumínio anodizado.
3.2. TESTE DE CORRODKOTE – ASTM B-380 - Este teste também é usado para determinar a resistência a corrosão de deposição de cromo decorativo. É principalmente aplicado em cobre/níquel/cromo ou níquel/cromo em peças designadas para serviços severos. O teste é feito aplicando-se uma pasta contendo sais corrosivos nessas amostras em teste, permitindo-se a pasta secar e expondo as amostras em umidade relativamente alta por um tempo determinado.
3.3. SALT SPRAY (FOG) NEUTRO ASTM B-117 Este é um dos mais velhos testes acelerados ainda em uso. Para este, como os testes CASS acima, é usado uma câmara de vapores que vaporiza uma solução de cloreto de sódio a 5% sobre o trabalho, por um tempo específico. Este teste é menos severo que o teste CASS. É principalmente usado na indústria de eletrodeposição de zinco e outras áreas de deposições decorativas onde a resistência à corrosão é exigida, mas, a atmosfera na qual a peça é sujeita no uso real é menos severa. Geralmente o tempo de exposição para obter o mesmo grau de corrosão é maior no teste de Salt Spray do que seria no teste de CASS ou teste de Corrodkote. Este teste não é considerado aplicável pela ASTM para o estudo e teste de níquel decorativo/cromo; cobre/níquel/cromo sobre ferro ou zinco diretamente em suas superfícies e ainda em eletrodeposição de cádmio em ferro.
Em alguns casos, neste teste, é usado uma concentração diferente de cloreto de sódio. A variação mais comum nesse teste é de 3% ou 20% dessa solução de sal, mais adequadamente 5% foi estabelecida como modelo.
3.4. TESTE DE UMIDADE Este teste não é nada mais do que expor as peças a uma atmosfera de alta umidade relativa de 90 a 100% por um determinado período de tempo.
Este é um teste muito suave e muito usado para deposições de zinco ou conversões de camadas.
3.5. TESTE DE ÁCIDO ACÉTICO SALT SPRAY ASTM B-287 - Este teste antecedia o teste CASS e uma vez que o CASS provou ser o mais eficiente, especialmente para depósitos níquel/cromo e cobre/níquel/cromo, seu uso diminuiu consideravelmente ATÉ SER COMPLETAMENTE DESCONTINUADO EM 1988.
3.6. TESTE FACT – ASTM B-538 Aplicado com um rápido teste de aceitação de controle de qualidade eletroquímico para camadas anodizadas decorativas e protetivas sobre alumínio e suas ligas.
O teste utiliza um aparato similar ao teste Kocour. O alumínio é o catodo e a platina o anodo em uma solução eletrolítica de cloreto de sódio. Durante o teste as camadas anódicas deterioram e a tensão celular cai. A velocidade na mudança da tensão é a medida considerada para a camada. DESCONTINUADO POR COMPLETO E SEM SUBSTITUTOS EM 1987
3.7. O TESTE EC-ASTM (1977) Este é um teste de corrosão eletroquímica que produz uma rápida avaliação da característica da durabilidade da corrosão de cobre/níquel/cromo e níquel/cromo depositado em ferro e zinco diretamente. A peça a ser testada é posta a uma corrente de densidade anódica baixa em um eletrólito específico por um período de tempo predeterminado. O eletrólito é basicamente escolhido em relação ao metal base envolvido e o tipo de teste desejado. O número de sitos de corrosão formados é a indicação direta do grau de resistência à corrosão, depois pode-se esperar um teste de deposição específico . Este teste tem um uso limitado comercialmente, mas ganhou aceitação como um método de pesquisa.
A INTERPRETAÇÃO DOS RESULTADOS DE CORROSÃO
A interpretação dos resultados obtidos dos testes de corrosão é a mais fraca ligação da cadeia. Logicamente nenhum teste dá uma resposta clara se a peça irá ou não, quando galvanizada, com uma certa camada, resistir a corrosão em qualquer atmosfera. Infelizmente não é assim. Isto pode ser apreciado por uma série infinita de números diferentes de atmosferas corrosivas, cujas camadas podem ser expostas e essas mesmas atmosferas podem afetar uma camada diferente de muitos modos. Entretanto, seria impossível projetar um teste que satisfaça todas condições e todas as variedades de corrosão média, especialmente no campo de testes acelerados.
Através de um extensivo estudo feito pelas indústrias automobilísticas, em conjunto com a ASTM, houve descobertas favoráveis que correlacionam entre 16 e 22 horas o teste CASS ou Corrodkote, a um ano de exposição nas ruas de Detroit. Entretanto com o aumento do uso de cromo micro discontinuo sobre o níquel duplex, que necessitava de um tempo de exposição longo, os resultados obtidos do teste CASS e Corrodkote, tem-se tornado questionado quando correlacionado com o uso no dia a dia.
Uma questão que é muito colocada “Se a minha peça for exposta a 20 horas de CASS, quanto tempo seria equivalente em um Salt Spray Neutro para se obter um resultado igual? Não há meios de responder esta questão, a menos que um certo número de peças fossem realmente levadas a corroerem nas mesmas condições. A correlação é feita depois por análise de estatísticas. Através de testes extensivos de várias peças, tem havido uma visão justa da correlação entre testes específicos e os usos diários .
Esta correlação seria verdadeira somente para aquelas peças específicas e seus depósitos, e também o teste que foi aplicado. Justamente porque os depósitos variados tem uma determinada sequência em um tipo de teste de corrosão, isto não necessariamente significa que eles irão se comportar da mesma maneira quando testado convencionalmente de outro modo.
Muitos testes específicos de corrosão tem sido usado por compradores ou por fabricantes como um controle de qualidade de aceitação e para estabelecer limites. Novamente estes limites são somente satisfatórios para testes específicos requeridos.
Uma outra questão que é frequentemente feita : “A minha peça passou no teste ?”. Novamente, a menos que haja uma descrição definitiva para o que esta passando ou falhando, a questão não pode ser respondida. Algumas especificações determinam nenhuma corrosão dentro de um tempo específico; outras abaixo de uma certa porcentagem de corrosão durante o mesmo tempo. Também deve ser estabelecido se somente as falhas no metal base os defeitos na superfície em geral tais como: aspereza, rachadura, dureza, etc. são levados em conta quando da aceitação ou rejeição da peça .
Um outro ponto a ser estabelecido, é se toda a superfície da peça é considerada significante quando determinada a área de corrosão. Muitas vezes dentro das peças ou áreas que são subsequentemente pintadas, por exemplo, pontos de corrosão não são considerados. Isto, entretanto é importante para se compreender completamente as especificações que são seguidas e saber que somente o comprador irá ou não aceitá-las.
Os testes de corrosão não são tão simples como parecem a primeira vista, pois existem uma multiplicidade de variáveis que precisam ser controladas. Uma completa compreensão do teste de corrosão é importante. Enfim, é importante a aquisição do conhecimento de como interpretar os resultados, a fim de se obter a informação desejada. Seria de grande ajuda se a maioria dos técnicos no campo de acabamento metálico, adquirissem os documentos citados da ASTM e familiarizar-se com os seus conteúdos e critérios.